重要なポイント
- 顧客依頼から数日以内に、複数の機能試作品の製作、テストを繰り返し実施
- 従来の試作ツールでは8週間要した製品開発期間をCarbon DLS™プロセスにより3日に短縮
- 大規模なライン試験用の金型を顧客依頼から数日で立ち上げ
組立技術の世界的な業界リーダーとしてARaymondは、顧客が生産ラインの非効率性を改善する革新的なソリューションを開発するには、迅速な行動が重要であることを理解しています。Carbon Digital Light Synthesis™(DLS™)3Dプリント技術とエンジニアリンググレードの3Dプリント材料を用いた迅速な設計改良と機能試作品テストにより、ARaymondは数週間ではなく3日間でより高性能のファスナーを製作し、自動車OEMメーカーの作業員の組立作業改善を支援することができました。
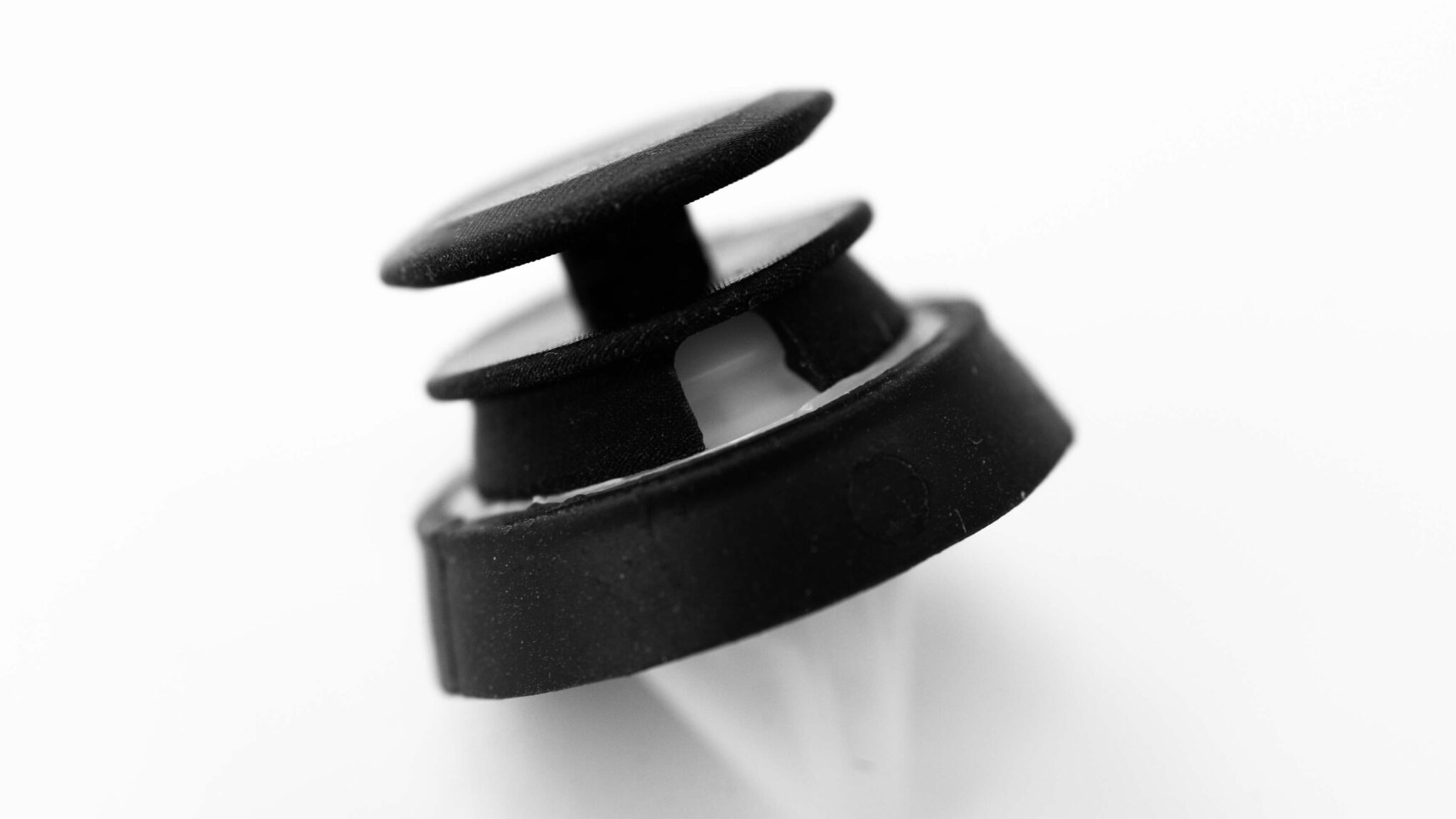
Carbon DLS™プロセスで生産したトリムクリップファスナーのボタン部分(機能試作)は数日で製作され、ARaymondの自動車OEM顧客に納入
ARaymondは複雑な組立システム用ソリューションの設計、エンジニアリング、製造を行い、金型を不要とし、人間工学に基づき組立ラインの改善と製造の合理化を図り、保守を容易にしています。さらに、世界各地のARaymond製造施設はISO 14001の認証を受けており、さらに全ての自動車部品工場はIATF 16949の認証を受けています。
課題:迅速、柔軟、かつ機能的な生産ソリューションの模索
ある自動車OEMメーカーがARaymondに相談した課題は、オペレーターが生産ラインのスピードについていくのを阻害するような難易度の高い固定作業でした。トリムクリップファスナーは、自動車のリフトゲートパネルの裏側に位置するため、オペレーターは頭上での組立作業となり、対応する穴に適切にはめ込む必要があります。一見簡単そうですが、実はファスナーの挿入力と引抜力の間には非常に微妙なバランスが求められます。
挿入力はオペレーターの作業性に、引抜力は自動車メーカーから要求されるファスナーのパネル保持力と保守性(何度でも取り外せること)に影響します。(ARaymond製ではない)既存のトリムクリップファスナーは組立に175N以上の力を要し、これは最大許容値(60N)の約3倍でした。さらに、このファスナーは最低150Nの引抜力を有し、組立中に部品が飛び出さないよう側面荷重に耐える必要がありました。
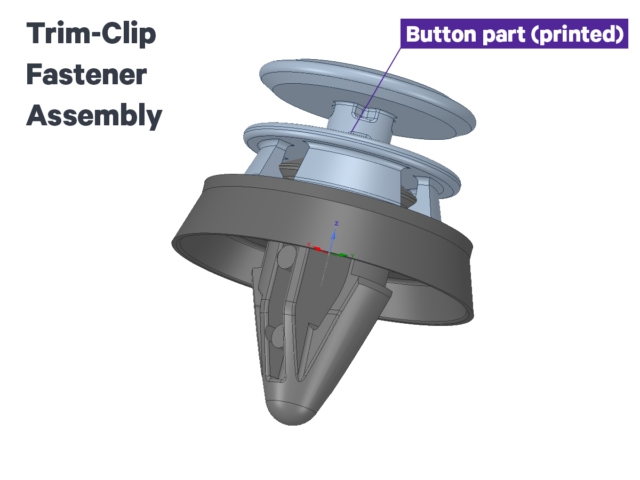
ARaymondはCarbon DLS™プロセスを用いて「ボタン」部品のデザインを迅速に改良
パネル組立時のオペレーターの苦労から、既存ファスナーの挿入力が大きすぎることが判明しました。また、複数の性能要件を考慮すると、新しいファスナーの設計にはバランスが求められました。ARaymondは引抜性能と側面荷重性能双方の維持と、挿入力の低減を単一のデザインで実現する必要があったのです。このファスナーに関する問題が自動車OEMメーカーの生産ラインを妨げ続ければ、1日のダウンタイムは数千ドルのコストに相当するため、ARaymondは顧客サポートのためには早急の対応が必要と考えました。
「このプロジェクトは切羽詰まっていましたが、社内でCarbon DLS™プロセスを活用できたために、ARaymondはより良いソリューションを顧客にタイムリーに提供できるようになりました。」
Sean Nagar
ARaymond エンジニア(自動車メーカー常駐)
ソリューション:迅速な設計改良
従来の金型アプローチでは、ARaymondチームはテストするオプションごとに1つずつ、3つのインサートを持つ試作金型を製作しなければなりませんでした。この金型作成コストは約16,000ドルであり、評価用部品の入手に要する期間は約8週間を要しました。
ARaymondは設計の繰り返し改良に適したCarbon DLS™技術を利用して、単一のデザインが全ての条件を満たすまで、コスト効率良く継続的な設計の改良を行いました。金型費用が不要となり、ARaymondは数日で機能試作品を顧客に提供することができたのです。
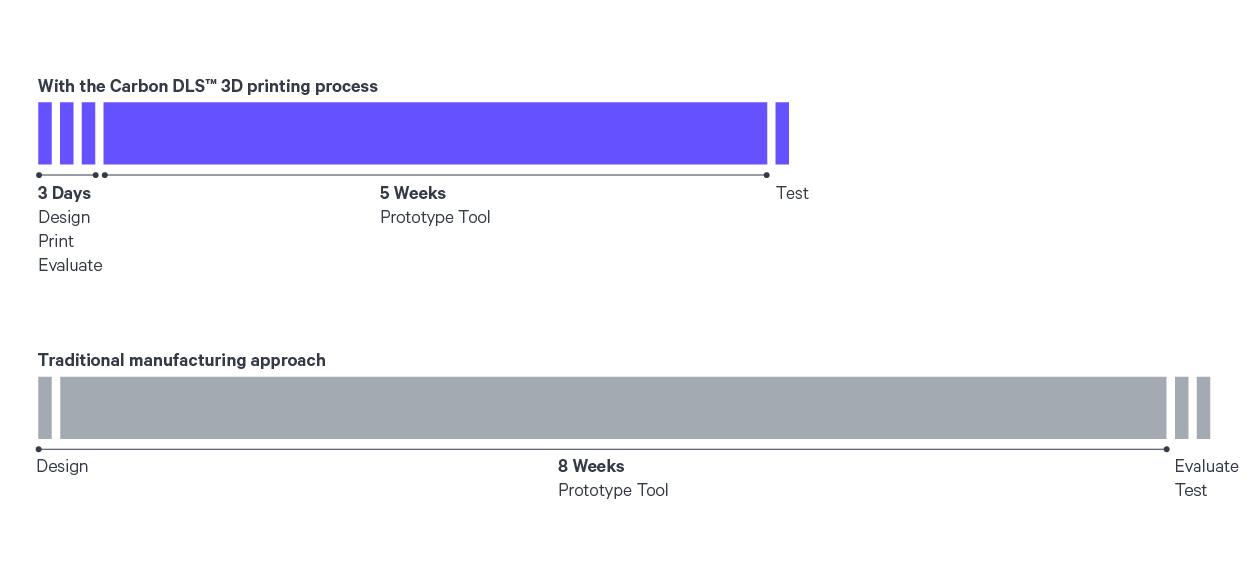
Carbon DLS™プロセスで短縮された所要期間(上)従来の射出成形による所要期間(下)。
ARaymondチームは、要件を満たしそうな様々なデザイン案をブレーンストーミングした後、各デザインの特徴が製品全体の性能に与える影響を評価する一連の実験を考案しました。ARaymondの先端開発部門に各デザインを具体化したCADモデルが送られ、Carbon DLS™プロセス用に様々な部品デザインが最適化されました。
高性能の3Dプリント材料
ARaymondチームは、Carbon RPU 70という硬質ポリウレタン3Dプリント材料が、この高性能ファスナーに最適であることを見出しました。この部品の生産に従来使用されていたエンジニアリングプラスチック、ポリオキシメチレンの寸法性能や機械的性能と最も一致していたためです。
ARaymondは最適化によって複数の部品デザインを完成させ、プリント時間の最短化と材料使用量の最小化を図りました。そして、部品はCarbon M2 3Dプリンタで一晩のうちにプリントされたことにより、ARaymondの貴重な業務時間を節約し、Carbonの迅速な稼働による優れた価値を示したのです。
翌朝出勤したARaymondチームは、オプションごとに50個の部品を用意し、顧客用途向けに並列で比較できるようにしました。Carbon RPU 70のエンジニアリンググレード品質により、ARaymondは機能試作として利用できる最終用途部品を顧客に提供することができたのです。
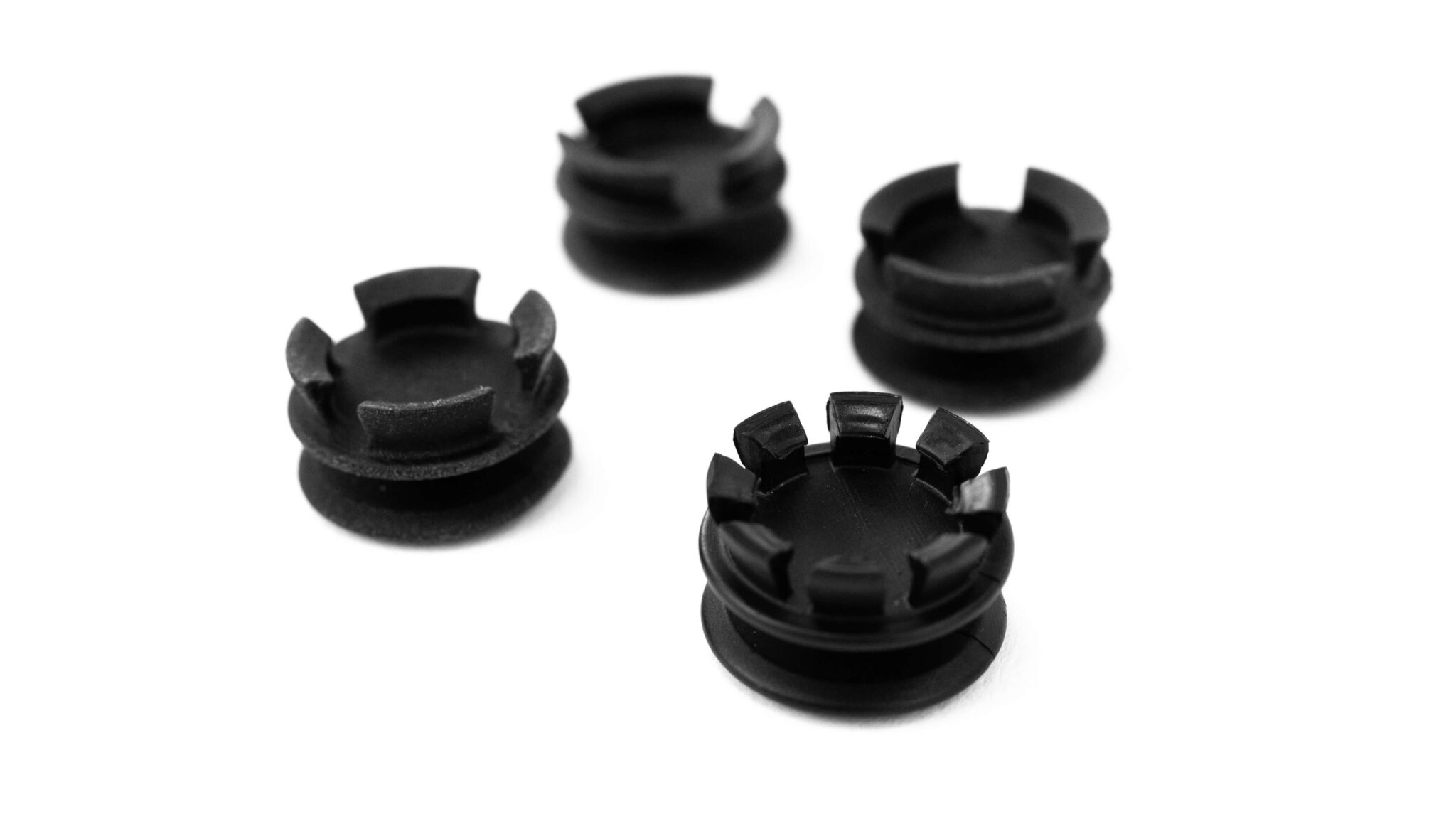
Carbon DLS™プロセスでプリントしたボタン部品の設計改良
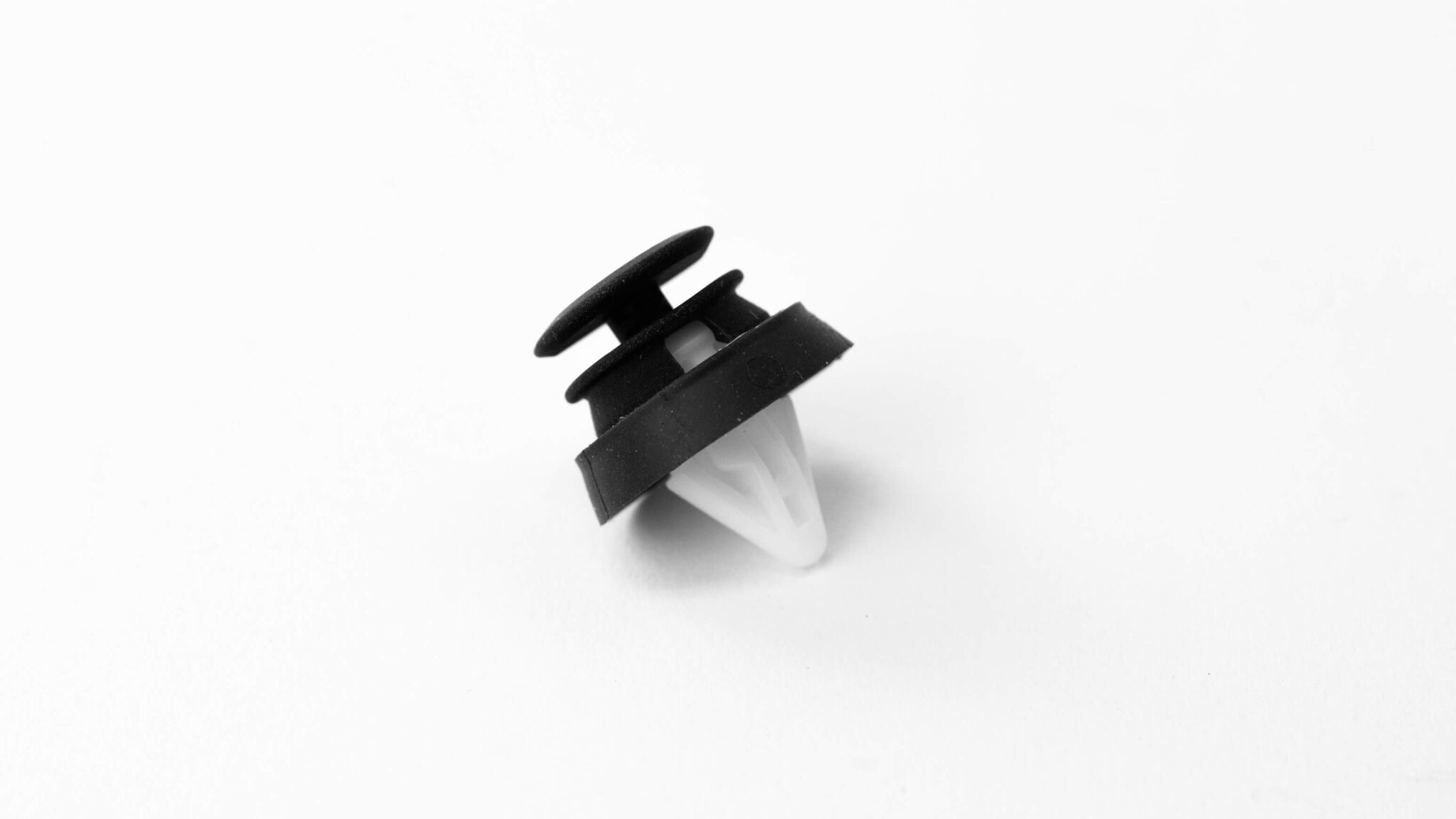
組立済トリムクリップファスナーの機能試作品
3日後:実際の部品が顧客の手に
顧客である自動車OEMメーカーは、ARaymondがわずか3日間で、顧客条件によりすぐテスト可能で且つ潜在的課題を解決しうる3つの有力なデザイン案を含む、リアルで機能的な部品が既に準備されていることを知って喜びました。その後、両社のエンジニアが協力して各案の評価を行い、それぞれの挿入、引抜、側面荷重性能を測定しました。3日目の終わりには、共同チームはファスナーに関する課題を解決するオプションを選び、生産を再開できることを確信したのです。
成果:製品開発のスピードアップ
ARaymondはCarbon DLS™プロセスを利用して、生産用部品を一晩のうちに納品することによって、顧客に数週間ではなく数日でソリューションを提供し、製品開発期間を大幅に短縮しました。ARaymondチームは最終デザインが固まったことにより、速やかに少量生産用金型を立ち上げることができました。この金型によって5週間以内により大規模なラインテストに必要な部品を生産することができました。ラインテストは3回実施され、全てが見事に合格しました。
設計を迅速に改良し、機能試作品を製作し、最終部品をコスト効率良く少量生産する能力を持つARaymondは、顧客の様々な問題を解決し製品開発を加速する柔軟な生産ソリューションとして、Carbon DLS™プロセスの活用に期待しています。