重要なポイント
- rpmは、Carbon DLS™技術を使用して、自動車向けリビングヒンジ代替のブリッジソリューションの開発に必要なコストと時間を削減しました。
- 高強度特性とコスト効率の良さからCarbonのエポキシベースのエンジニアリング材料EPX 82が選定されました。
- Carbon DLS™技術で生産された部品は、最初から射出成形品並みの品質でプリントされます。
独Helmstedtのrapid product manufacturing GmbH(rpm)は、少量の特殊部品や機能試作品を製造しています。rpmは23年以上、射出成形による連続生産に移行する前の「つなぎ(ブリッジ)」として11の異なる技術を用いて、プラスチックの少量生産部品や機能部品を生産してきました。ブリッジソリューションはプロジェクトの開発コストを予算内に抑え、また顧客が少量生産部品を生産する手助けとなっています。
しかし、連続生産用の射出成形金型の開発には、設計変更、コスト、時間の遅延がつきものであり、最適化の余地があります。
rpmはCarbonのDigital Light Synthesis™(DLS™)3Dプリントプロセスをいち早く採用し、欧州のある自動車メーカー顧客と共同で、金型設計の改良プロセスを改善するという課題に取り組むことにしました。
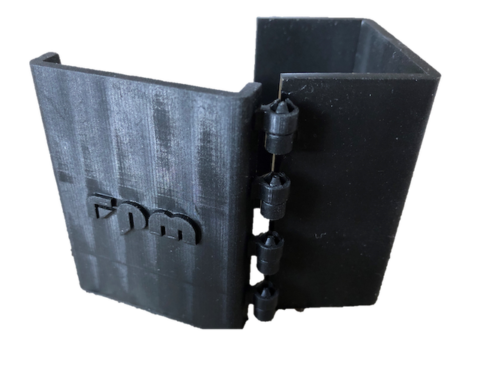
Carbon DLS™を用いたリビングヒンジ代替モデル
デザインを見直し、コストと時間を削減
rpmが特に関心を示したのは、比較的複雑な形状のエンジンルーム内の小さなケーブルダクトやブラケット、ホルダー類でした。
これらの部品には通常フィルムヒンジが使用されているため、作業者が配線してスナップで閉じることができ、また複雑な内部空洞を有する単一の部品とすることができるようになっています。
このようなケーブルホルダーは、特にリビングヒンジ部分を含む部品全体ではサイズが大きくなるためCarbon DLS™プロセスでの製造には適してはいません。
さらに、この部品には3つの異なるヒンジがあるため、プリンタのプラットフォーム上に部品を最適に配置可能な方向がありませんでした。
Carbon DLS™プロセスを利用する利点の1つは、材料の選択肢があることです。Carbon RPU 130はこの用途に必要な耐熱性とIMDS認証に対応可能な3Dプリント材料です。
しかし、生産コストを削減して顧客の目標価格を達成するため、材料は同様な強度を持つエポキシ系エンジニアリング材料であるCarbon EPX 82が選定され、設計はその材料に最適化したものとなりました。
自動車部品メーカーと協議した結果、Carbon DLS™プロセスによる生産に適した再利用可能なデザインプロファイルを有し、機能テスト時に最終部品の性能を模倣可能な方法として、フィルムヒンジをはめ込み式のコネクターシステムに置き換えるというコンセプトが発案されました。
「Carbon DLS™プロセスは、最初にプリントした部品から射出成形並みの品質を実現できるという点で、アディティブの中でも際立っています。
これにより、量産に向けた迅速な立ち上げやアフターマーケット部品の提供など、新たなアディティブマニュファクチュアリングの利用シーンが広がります。
Carbon 材料は、連続生産に求められる多くの厳しい評価基準に耐え、生産時間とコストの両方の大幅な削減につながります。rpmでは、必要な部品生産量に応じてCarbon DLS™プロセスと従来の射出成形との間をシームレスに移行する道が開かれつつあると考えています。」
Dr Claus Thomy
rpm 営業担当役員
Carbon DLS™プロセスによるデザインと材料の融合
rpmのデザインチームは、生産用にフィルムヒンジを別々の部品に分割し、デザインの重要な要素を入れ替えました。最初のテストラウンド後、rpmと顧客はコスト削減以外の利点に気付き始めました。
部品を分割することにより、部品の一方のみの設計を改良するときに他の一方を再利用できるようになり、必要なプリント時間と材料を半減させることができました。
また、Carbon DLS™プロセスでは複数のデザインを同時にプリントしてテストすることができるため、デザイン修正を迅速に行うことが可能です。

標準的なデザインプロセスとCarbon DLS™プロセス手順の比較
Carbon DLS™プロセスを使用するもう一つの主な利点は、Carbon EPX 82材料がIMDSに登録され、最終用途の自動車部品向けに承認されていることです。
これにより、テスト段階で実用的な結果が得られ、他の方法で部品を製造する際のシミュレーション作業が容易になりました。Carbonの2液性材料群は他の3Dプリント技術にはない強力な優位性をもたらしているのです。
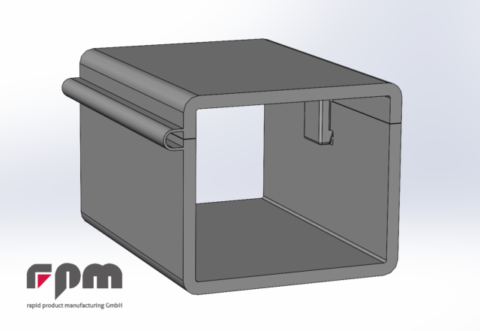
標準の射出成形リビングヒンジ/フィルムヒンジ設計
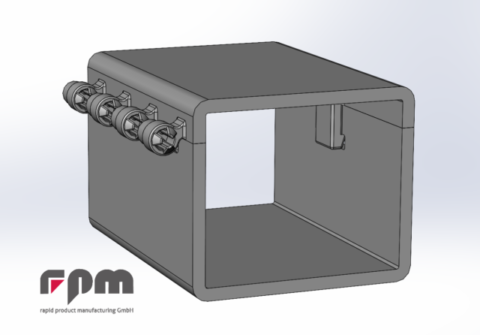
射出成形ヒンジ設計を模倣するためにCarbon DLS™プロセスを使用して作成されたコネクタシステム
Carbon DLS™プロセスのプラスチック部品成形技術ポートフォリオへの適合性
2018年にrpmが初めてCarbon DLS™プロセスを技術ポートフォリオに追加した際、rpmは生産スピードがこの技術の主な利点の一つだと考えました。幾つかのプロジェクトを経た後rpmは、Carbon材料の選択肢もまた、より重要な価値ドライバーだと考えるようになりました。
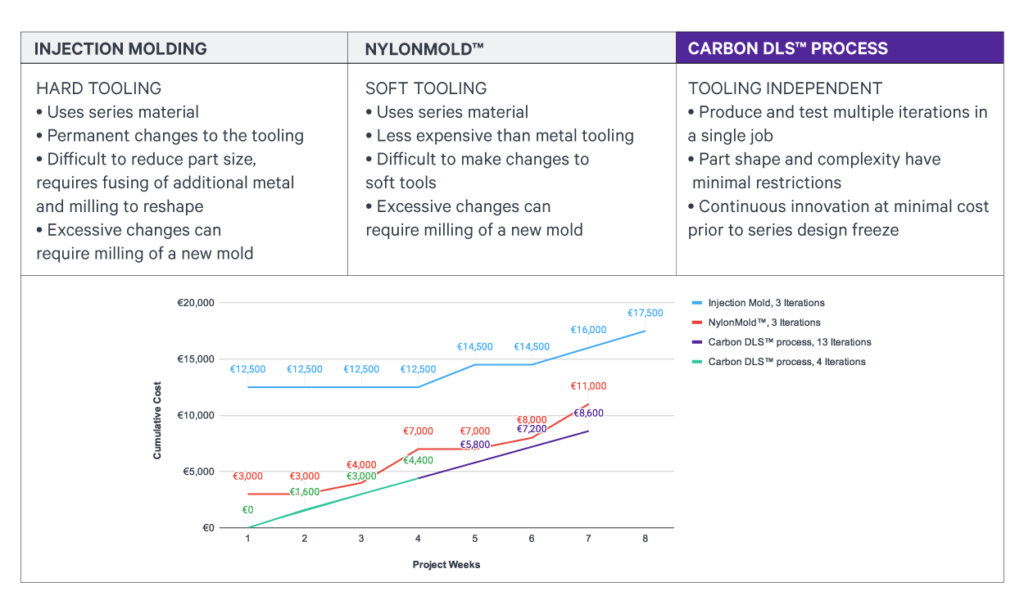
上記コスト例は比較用参考条件によるもの。最終的なコストは、サンプル部品の数、金型サイズ、変更の複雑さ等によって変動
Carbon DLS™プロセスは他のアディティブマニュファクチャリング技術と比較して、多くの設計上の留意点が従来の射出成形方式と類似しています。
例えば樹脂の流れを考慮することは、射出成形用の金属金型内のキャビティや形状を予測することに類似しています。
このことはrpmの技術ポートフォリオやプラスチック部品の設計プロセスの強化という観点で、非常に重要な役割を果たしています。
「Carbon DLS™は少量量産向けの重要な部品群をカバーしています。rpmは追加の金型なしで、最終用途に使用する材料から複雑で小さなサイズの部品を生産しています。これは当社が保有する10種類のプラスチック加工技術の間の重要なギャップを埋めるものです。
このDLS™適用事例では、スピードを上げてプロジェクト全体のコストを削減しながら、設計改良の回数を増やしています。量産用樹脂相当の材料を使用しているため、アディティブマニュファクチャリングはさらに、製品ライフサイクルの中に組み込まれるようになりました。
このような500~2,000個ロットの部品での用途が着実に増加しており、DLS™に最適な領域であることが証明されてきています。」
Dr Jörg Gerken
rpm 技術担当役員