Specializedは1974年の設立から1つの目標を掲げてきました。サイクリストの生活向上を目指し、革新をもたらし、刺激を与えるということです。Carbonプラットフォームの利用により、Specializedはサイクリストにまん延する課題に対処する新たな方法を発見し、それを従来の開発プロセス対比2倍のスピードで実施しました。
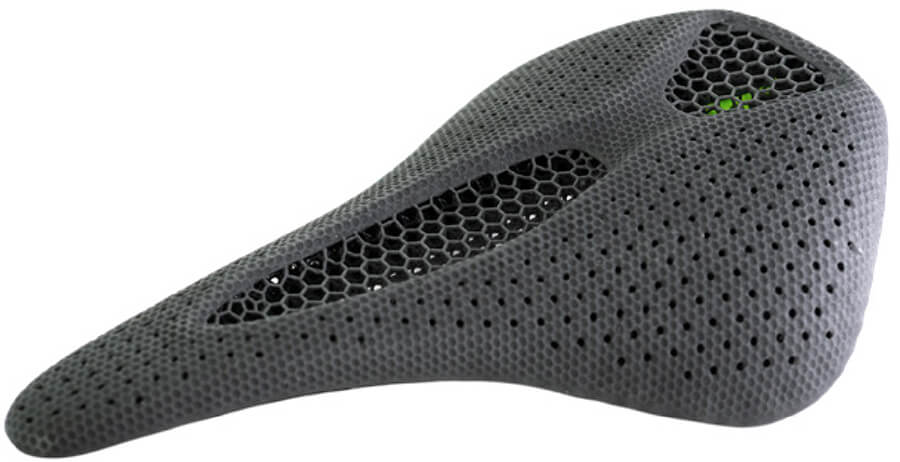
図1:Carbonプラットフォームで製作したSpecialized S-Works Power Saddle
課題
あらゆる水準のサイクリストにとって、自転車サドルは、サイクリングの最も重要な側面の一つです。自転車に乗らなくなる理由として乗り心地が悪いことがよく挙げられているように、乗り心地の良さはサイクリストにとっての性能なのです。Specializedは20年以上にわたって、新製品によってこの問題に対処してきましたが、異なる種類の発泡材を用いる伝統的な製造方法は、ほぼ実用面での限界に近づいています。
Specializedの従来の代表的な自転車サドルは、3種類の発泡材を組み合わせて、様々な機能ゾーンごとに異なる剛性をもたせて機能向上を実現してきましたが、Specializedがそれ以上ゾーンを増やす実用的な方法は見出せませんでした。
Specializedは乗り心地と安定性を両立させ、最高のパフォーマンスを発揮する自転車サドルを製作する必要がありました。但し、サドル密度の変動に無限に対応する材料と、理想的な乗り心地を提供するゾーンを作る製造プロセスの二大要素が欠けていたのです。
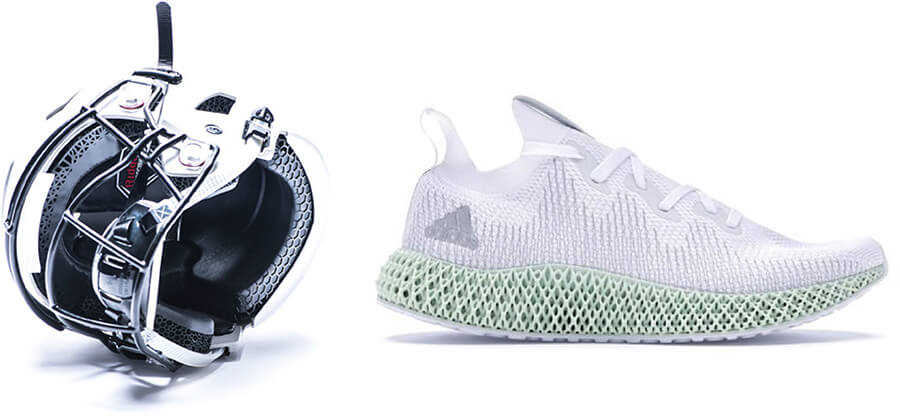
図2:様々なラティス構造 衝撃吸収用(左) 反発用(右)
測定と乗り心地の良さ
プレミアムな高性能自転車サドルの設計は、第一原則に立ち返ります。サイクリストの乗り心地を良くする原動力となる設計要素は何でしょうか。Specializedは、製品・市場適合性の理解を深める新たな手法を構築するために、3D製造技術をどのように活用できるのでしょうか。
衝撃吸収か反発か?
Carbon EPU樹脂を使ったエラストマーラティスは、引裂強度、反発特性、伸びを組み合わせて、クッション性、衝撃吸収性、防振性を最適化しているため、この用途に適しています。
はたして、乗り手は衝撃吸収性と反発特性のいずれを重視するのでしょうか。この問いに答えるため、SpecializedはCarbon技術を使って2種類の異なる材料(衝撃吸収性、反発特性それぞれを最適化)により同じデザインのサドルを作成し、テストを行いました。
直観的には、衝撃吸収を増した方がスムーズな乗り心地をもたらすように思えますが、実際には、衝撃を吸収するとシートはゆっくりと圧縮し、乗り心地が悪くなるのです。サイクリストは、明らかに姿勢を保持できる反発特性を重視したのです。
乗り心地か、コントロールか?
これらを両立できるのなら、なぜいずれか一方を選ばなければならないのでしょうか。Specializedは、簡単に圧縮するゾーンを設けて乗り心地を改善しながら、サイクリストにとって安定性と血流の助けとなる一定のサポートと圧力が必要との理論を立てたのです。この理論に焦点を合わせた最初のデザインでは、サイクリストの座骨用の柔らかくて、大きなくぼみを作成しました。テスト結果によると、ゲルサドルがしばしば連想されように、柔らかさが均一だと不安定になり、乗り手がコントロールを失ったのです。これに対処するため、Specializedは、ティアドロップ(涙のしずく型)ゾーンにて、座骨を中心部の柔らかいところに置き、徐々に硬さが増加するように圧縮を変化させました。その結果、乗り心地を改善するために圧力を最適に分布させながら、サイクリストが必要とする最高のコントロールを実現するといった完璧な組み合わせとなったのです(図3)。
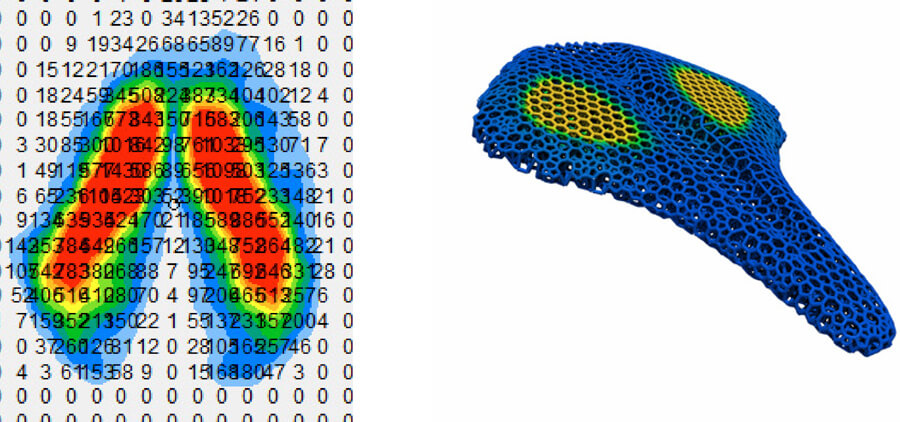
図3:圧力分布図の例(左) 圧力分布と安定性向上を最適化した乗り心地の良さを実現した自転車サドルのラティス構造
From File to Road
エンド・ツー・エンドプロダクトソリューション
SpecializedはCarbonプラットフォームを活用することによって、より緩やかに圧力を分布させつつ圧力のピークは低くするというサイクリストの要求に完璧に合致するエラストマーラティス製自転車サドルを開発し、これを量産化することに成功しました。
更にCarbonはエキシマ光源を使った新しい技術を開発し、テイラーメイドの微細なトポグラフィを設計し、高品質マット仕上げにより最適な表面グリップをサドルに付与しました。これは、商業用途の3D造形用途では初めて使われる技術です。
乗り心地のブレークスルー
Carbonプラットフォームにより、Specializedは24か月を要した従来の開発期間を最終的には13か月に短縮しました。新しい自転車サドルの開発期間としては最短です。
調査+技術的実現可能性 | |
---|---|
期間 | 1か月 |
改良検討 | 10デザインサイクル |
達成基準 |
|
アルファ:プルーフオブコンセプト | |
---|---|
期間 | 6か月 |
改良検討 | 40デザインサイクル |
達成基準 |
|
ベータ:デザイン検証 | |
---|---|
期間 | 5か月 |
改良検討 | 30デザインサイクル |
達成基準 |
|
パイロット:生産開始 | |
---|---|
期間 | 1か月 |
改良検討 | 仮決めしたデザインを検証し、アッセンブリを改善する変更を実施 |
達成基準 |
|