Carbon M2 採用事例
SWANSは山本光学株式会社が展開するスポーツ用のゴーグルやサングラスなどを製造するスポーツアイウェアブランドだ。2019年バレーボールの鍋谷友理枝選手の専用モデルをCarbon社の3Dプリンターを使って製造した。そこには非常にドラマティックな開発秘話が隠されていた。JSR社主催ウェビナー、山本光学開発陣へのインタヴューなどを通じて取材した、いま日本のモノづくりで起きている変革に関してご紹介したい。(取材:シェアラボ編集部 提供:JSR株式会社)
『次に眼に当たったら失明』鍋谷選手を守るゴーグルづくりへ
日本を代表するバレーボーラーである鍋谷選手は、リオに続いて東京オリンピックへの出場権をかけて挑戦を重ねてきた。そんな中で、練習中に鍋谷選手の眼にボールが直撃する事件が起こる。スポーツドクターの診察を受けた鍋谷選手だが、「次にボールが眼を直撃すると失明する恐れがある」と厳しい診断結果となった。その医師から紹介され、スポーツゴーグルを展開するSWANSの直営店を鍋谷選手が訪れることになる。直営店を訪れた鍋谷選手は既製品のスポーツゴーグルを手に取り、より視野角が広いモデルがないか尋ねたという。どうしてもオリンピックに出たい。眼を守りながら、世界で戦うためのゴーグルが欲しい。そんな熱意を受けて、山本光学は鍋谷選手専用モデルの開発を決定、プロジェクトがスタートする。
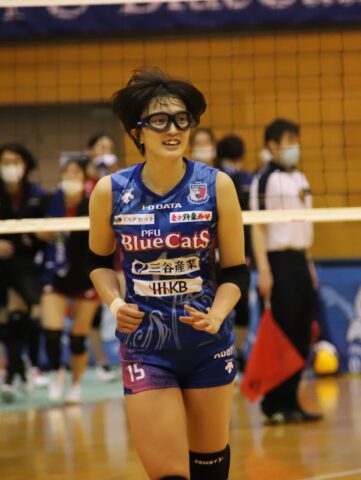
PHOTO: PFU Blue Cats
通常12か月かかる製品開発を3か月弱に圧縮した舞台裏
通常、山本光学では、新製品の開発は約1年かけて行う。しかし9月に行われるワールドカップまで残された時間は3か月を切っていた。ちょうど鍋谷選手の訪問の直前にCarbonと接触していた山本社長は、この話を受けてすぐにCarbonに連絡を入れる。従来の開発方法では到底間に合わないが、3Dプリンターから直接最終製品を造形できるCarbonであれば、なんとかなるのではないか。
「Carbon社とJSR社が出展していた展示会ブースでは、造形されたアディダスのミッドソールやアメフトのヘルメットなど実際に造形されたサンプルが展示されていました。柔らかく弾力性のある樹脂は私たちのモノづくりでも利用していたのですが、特性が似ていると感じました。(山本光学 デザイナー 富永浩史氏)」
手ごたえはあった。あとは実際に現場を見てみたい。

山本光学 山本社長
山本光学がアメリカで見たもの
Carbonの日本でのマーケティングを担うJSRはアメリカのCarbonの工場見学を山本光学に提案した。「工場には実際の3Dプリンターだけではなく、アプリケーションエンジニアをはじめとしたAMでのモノづくりを推進できる体制があります。実際に目で見て体感していただければと思い、ご紹介しました。(JSR 銅木 克次氏)」
その場で山本社長はすぐにアメリカ視察を決意。当初単身で渡米しようとしていたが最終的に4名の開発者でCarbonの工場に乗り込むことに。渡米は日数的にも費用的にも負担になる。すぐに行こうと思った理由はなんだったのか。
「私たちは“打ち合わせは対面で”という文化でしたので(笑)、現地で生産される様子を確認したり、一緒にお仕事をする方とお会いしたいと思いました。工場内での生産風景などを見学させていただき、実際に大量生産を行っている様子を見て、大きな手ごたえを感じました。(山本光学 山本氏)」
「現地では実際にCarbonの3Dプリンターを使って大量生産される最終製品を目にすることができました。また実際に設計支援を行ってくれるアプリケーションエンジニアとの意見交換の場も設けていただきました。いままで社内では形状確認のために3Dプリンターを利用していましたが、最終製品には利用してこなかったので、不安はありましたが、サブスクリプションでこうした支援を受けられるのであれば、やれると感じました。(山本光学 富永氏)」
協業レベルの開発コミット体制 ―Carbon独自のサブスクリプション
日本を代表するバレーボーラーである鍋谷選手は、リオに続いて東京オリンピックへの出場権をかけて挑戦を重ねてきた。そんな中で、練習中に鍋谷選手の眼にボールが直撃する事件が起こる。スポーツドクターの診察を受けた鍋谷選手だが、「次にボールが眼を直撃すると失明する恐れがある」と厳しい診断結果となった。その医師から紹介され、スポーツゴーグルを展開するSWANSの直営店を鍋谷選手が訪れることになる。直営店を訪れた鍋谷選手は既製品のスポーツゴーグルを手に取り、より視野角が広いモデルがないか尋ねたという。どうしてもオリンピックに出たい。眼を守りながら、世界で戦うためのゴーグルが欲しい。そんな熱意を受けて、山本光学は鍋谷選手専用モデルの開発を決定、プロジェクトがスタートする。
![]() 鍋谷選手の顔のスキャニングデータをもとにモデル化 |
![]() 開発初期の設計を実際に造形した試作。硬い材料と柔らかい材料を組み合わせている。 |
通常12か月かかる製品開発を3か月弱に圧縮した舞台裏
帰国後、すぐに契約を決意。3Dプリンターが社内に納品される間も惜しんで開発がスタートした。山本光学側の対応も急ピッチで進められたが、Carbonのアプリケーションエンジニア側も設計段階から協業したという。
「鍋谷選手が練習している体育館に伺いまして、椅子に座っていただき、顔の形をスキャニングしました。持ち運べるハンドスキャナーを使って私が測定しまして、その顔のデータを元に、最適な形状に調整していきました。(山本光学 富永氏)」
「ほぼ毎日のように山本光学さんと連絡していました。直接オフィスにお伺いしてアメリカと繋いで会議を行うこともありました。インド人の優秀なアプリケーション・エンジニアが設計支援に入ったのですが、最初の3Dモデルのクッション構造部分は彼が用意してくれました。(JSR銅木氏)」
山本光学は社内で3Dモデル設計を行う能力がある。しかし限られた時間の中で、スポーツゴーグルを完成させるために、Carbonが動いた形だ。しかもそこに追加費用は一切発生していない。
Carbonのサブスクリプション契約では、AMでの前工程、造形工程に関する広範なサポートを約束しているが、それが実際に機能していた。
設計モデルを3Dプリンターのメーカーが用意するというのは非常に特異なケースのように感じられる。その点を伺うと「なぜJSRさんやCarbonさんはこんなに協力してくれるのか、正直不思議でした。これで商売になるのかこちらが気になるくらい、一緒にモノづくりを行っていましたから(山本光学 富永氏)」
「サブスクリプション契約の本来の意味は、機器のリース契約や保守契約とは本質的に異なります。実際に機材を運用し、設計から開発までモノづくりをするお客様のプロセスそのものの変革をお手伝いすることだと考えています。これは今回特有の体制ではなく、Carbonが
世界中で行っているサービスです。私たちはご一緒するお客様の熱量をきちんと成果につなげるお手伝いを行っているだけです(JSR 銅木氏)」
銅木氏の静かだが自信に満ちた回答に凄みを感じた。
最終製品と同じ製造方法だからこそ試作改善が最終品質の改善に直結
こうしてCarbonの強力な支援を受けながら、山本光学でのモノづくりが着々と進む。
「通常の製品開発は1年がかりで、金型を使用した試作も1,2回しか行いません。今回の鍋谷選手モ
デルは3か月弱の中で試作を7,8個作っています。(山本光学 富永氏)」
ほぼ毎週試作造形を行い、そのたびに鍋谷選手に着用感を聞く。最も重要視されたのが、安全性の確保だ。山本光学ではASTM(アメリカ材料試験協会)で規定されるスポーツゴーグルの安全基準に従った試験を行っている。試作段階でも最終製品と同等の試験を行いながら、課題の洗い出しと改善を行っていった。試作品とは言え、Carbonの3Dプリンターは最終製造にも対応しているため、試作を通じて試験した内容を改善していけば、最終製品の品質向上に直結する。この点も開発期間を大幅に短縮できた点だ。
当初の鍋谷選手の希望であった広い視野角を確保できるように設計変更を継続した。さらにバレーボールは運動量が多い屋内スポーツ。選手が競技中にスポーツゴーグルを着用すると、汗でゴーグルが曇ることが分かった。その曇りを防ぐための空気穴を何度も調整した。
「ゴルフや野球のように屋外スポーツ向け製品の開発は経験があったのですが、屋内スポーツ向けのアイガードは初めての取り組みでした。ゴーグルの曇りに関しては最後まで修正を繰り返しました(山本光学 富永氏)」
こうした短いサイクルで理想的な形状と強度を模索できたのも、シミュレーションだけではなく実際の試作品を短いサイクルの中でなんども試験できたことが大きいという。「5回目の試作で、ほぼ形状的には決まったのですが、まだ少し曇りますね、とコメントをもらいました。最後の調整ということで、空気穴の形状を工夫して、試合に臨んでもらいました。(山本光学 富永氏)」その結果、鍋谷選手は後顧の憂いなくワールドカップに参戦し、日本代表として活躍することが
できた。
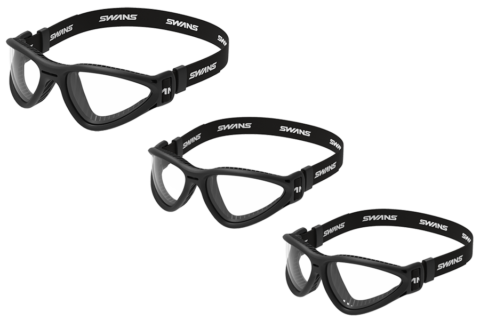
SWAN アイガードのサイズ展開
鍋谷選手の実力と努力がもたらした成果であることは間違いないが、その背中を支えたSWANS
のゴーグルと、短期間での開発を実現したチームの貢献は大きかっただろうと感じた。
今後は3Dプリンターならではのモノづくりを継続していくという事で、今回の鍋谷選手モデル
のアイガードは実際に市販される。サイズも子供用、大人用が展開される。
「今回の取り組みを通じてCarbonの3Dプリンターでできる事が理解できました。またそれ以
上に、もっとこんな事ができるんじゃないかというアイディアも沢山持つことができました。
3Dプリンターでしかできない事を通じてモノづ
くりを進めていきたいと思います。(山本光学
富永氏)」
「選手の安全を守ることを第一義に考えていますが、3Dプリンターならではのモノづくりで新しい価値を生み出していきたいと思います。(山本光学 山本氏)」
既に取り組みは始まっており、山本光学ではクラウドファンディングを通じた完成品重量わずか10g以下の超軽量サングラスの開発を行っている。選手生命を守るスポーツ用アイガードとは全く違うアプローチだが、着用感が気にならないほど極限に軽いサングラスにも3Dプリンターならではの設計アプローチが秘められているようだ。こちらは別記事でも取り上げているので、参照されたい。
従来の日本の3Dプリンター業界らしからぬ、特異な取り組み方
お話を聞きながら「なんだかドラマみたいだ」と思った。そう、昔よく見たプロジェクトXのような、熱いモノづくりがそこにあった。しかし何だろう。このモノづくりは3Dプリンターメーカーとスポーツメーカーが行うモノづくりとしてはなんだか特異な関係で実現しているもののような気がする。一般的には3Dプリンターメーカーは機器の販売が業務範囲だと思う。設計には立ち入らない。サービスビューロでもアドバイスこそすれ、設計変更を自ら行うことはない。なんだか特殊なことが起こっているぞ、と感じた。これは前回JINSがCarbonの3Dプリンターを利用して3Dプリントサングラスを製造販売している取り組みを伺った際にも感じた事だが「毎週定例ミーティングを行った。」「テストショットを週1回のペースで行った。」など、まるで共同開発を行っているパートナー企業や長年の取引関係にある系列企業との取り組みのように、濃密な協力体制を感じる。
こういう感触を得た事は今まで200名ほどの業界関係者を取材しても初めての経験だった。なんだか昔の日本企業と出入りのデザイン会社や加工会社が一緒にモノづくりを行っているような親密な関係性。サブスクリプションとは聞いていたが、この緊密な連携はいったい有償なのか、無償なのか。ウェビナーに登壇した一部の企業だけのものなのか、それとも他の利用企業とも同じような関係性を培っているのか、別途時間をもらい、JSRの銅木 克次氏に疑問をぶつけてみた。
モノづくりのどこまでを一緒に行っているのでしょうか?

ウェビナーで当時を振り返るJSR銅木氏
―ウェビナーを受講してみて、なんだか他の3Dプリンターの導入事例とは毛色が違うような印象を持ちました。まるで協業パートナーとの事例発表会のように、登壇企業が自然にCarbonや
JSRを語っている点が印象的だったんです。実際どこまで一緒にモノづくりを行っているか、伺ってみたいと思います。AMのプロセスには造形するためのデータ準備から造形、後加工まで
あると思いますが、協業の中身はどこまで及んでいるのでしょうか?
全部です。
―全部ですか?
はい。全部です。
―装置購入時におまけとして支援を行ったり、サービスビューロ的に、一部業務を追加料金をうけとって提供しているんですか?
勿論デザインはお客様のものです。また3Dスキャニングや後加工はさすがに別ですし、材料代は別途いただいていますが一部の設計代行、お客様の設計されたデータにラティス構造を埋め込むようなデータ処理、よりAMを意識したデータに修正していく作業は、すべてCarbonのアプリケーションエンジニアが、定額料金内でお手伝いしています。
―それは顧客の設計データをCarbonのエンジニアが加工したり修正しているという事ですよね?
はい、Carbonは社員が400人以上います。アメリカ駐在のアプリケーションエンジニアやAMに精通したソフトウェアエンジニアのリソースは、必要に応じてサブスクリプション契約の中で、利用可能なんです。アメリカで働くCarbonエンジニアをJSRが通訳しながら、作業してもらっています。こういうスケジュールで実際に行動するので、リソースが必要と交渉すれば、そのリソースが活用できます。
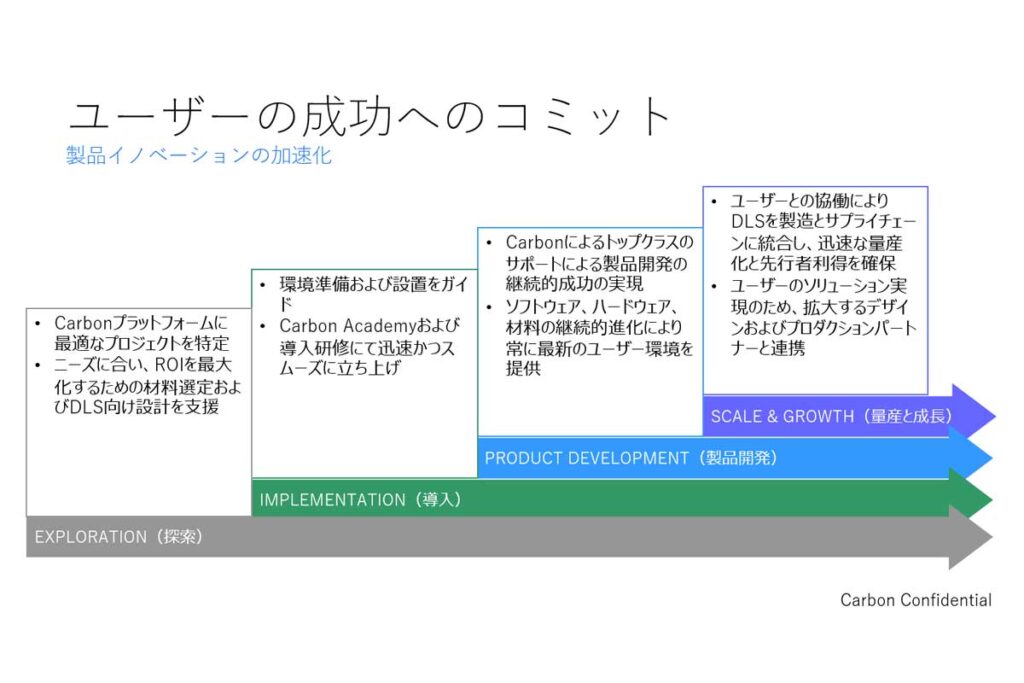
Carbonのサブスクリプションがめざすユーザーの成功
―なにか条件はあるんでしょうか?
特にありません。年間725万円で3年契約のサブスクリプション契約をCarbonと結べば、どんな企業様でも同じサービスを受けることができます。ですが、強いて言えば熱量が大きい企業、目標がはっきりしているプロジェクトが優先されます。「やるかどうかわからないけれど、念のため相談したい」「まだ経営層とコミットできていないので決定ではない」という状態ではリソースの限りもありますので同様の協力を得ることは難しいでしょう。「経営層とも握っているので絶対にあと2ヶ月でローンチする」のように具体的なゴールが明確で、企業として意思決定している場合、Carbonはリソースを惜しみません。意思決定できるChampionがそのプランにコミットしていれば、極論設計者がいないプロジェクトでも、デザインからサブスクリプション契約の範囲内でお手伝いすることもあります。
―設計者がいないという事は、利用企業が3Dデータを作れないということですよね。3Dモデルをサブスクの範囲で用意してもらえるのですか?
はい、すべてのケースがそうという訳ではありませんが、すでに日本でも2社推進中です。まだ公表できる段階ではありませんが、とても画期的で、インパクトのあるモノづくりをされている企業様の事例があります。両社とも、プロジェクトに3DCADを描ける設計者はアサインされていません。紙に書いたデザインイメージを元に、Carbonのアプリケーションエンジニアがモデルを起こすところから作業しています。
このサブスク、思ってたのと違う
Carbonの3Dプリンターをサブスクリプション契約すると、3Dプリンターに関しては、電気代と材料費等の消耗品以外にランニングコストがかからない。その上で、担当チームが付き、極端な例(そして先ほどの銅木氏の発言にあったように日本で実際に2社契約済みの事例がある)では、3DCADを操作できる設計者がいない場合でも、AMで造形する際に最大限の効果を生むようにラティス構造を埋め込むなど3Dモデルを設計し、シミュレーションで造形の妥当性の検証を行い、最も生産性が高い積み方になるように積層造形用のデータを用意してくれるという。字義通り見るなら、デザイン会社やサービスビューロが有料サービスとして提供している業務と同じように聞こえる。
―これはいわゆるサブスクリプションの中身なんでしょうか?
はい、Carbonの考えるサブスクリプションは、材料費などの費用は別ですが、3Dプリンターの利用、DfAMに基づく設計支援、造形準備など、3Dプリンターを利用したモノづくりのための業務の全ては支援対象です。
―これはサブスクであってサブスクじゃない気がします。3Dプリンターを買ったらサービスビューロがおまけで付いてきたような印象を受けますがが、、、
やりすぎ、なんでしょうかね?ですがサブスクリプションビジネスの本来の定義に従うと、私たちの行っている内容こそが正しいと思っています。材料以外の3Dプリンター、設計やデータに関する支援体制、造形パラメーターの最適化やもっとも適切な造形の方法のご支援、そのすべてを含み、カスタマーエクスペリエンスを第一に考えるのがサブスクリプションです。守秘義務などに縛られる企業様は自社で進めていかれますが、私たちを使いこなしてくださる企業様とは、パートナーとして一緒にモノづくりに取り組ませていただいています。
***
通常の3Dプリンターの導入では、製品としての3Dプリンターの設置や試験造形の実施、教育トレーニングを受ける事はできるだろう。機器の保守も受けることができるだろう。しかし別途で費用を払って依頼しているわけでないのなら、「こんな製品を作りたい」という狙いを聞いて、サンプルデータを設計してくれる3Dプリンターメーカーはいない。作ってみたデザインデータを元に構造の一部をラティス化したり、アプリケーションエンジニアの観点でデータを修正してくれることは料金外の別の仕事になる。そう、Carbonを除いては。
Carbonがはまる企業、はまらない企業
―言葉を選ばずにお伺いしますが、Carbonがはまる企業とはまらない企業の違いを教えてください。
導入がスムーズに進む企業の例を振り返ってみると、Carbonが得意とする柔らかい材料を活かしたモノづくりができる事、既存の設計を3Dプリンターで造形するだけではなく、AM(Additive Manufacturing)を最大限に活かせる設計変更にチャレンジできる事、経営層や意思決定者が明確に推進することを決めている事の3つが挙げられます。特に日本では最後の「経営層や意思決定者が明確に推進することを決めている事」が重要になってきます。
―意思決定者のコミットを重要視しているのはなぜですか?
新しい工法であるAMの推進で成果を上げるためには、設計変更が不可欠です。設計変更だけではなく材料を変える必要も出てくるかもしれません。試験方法を見直す必要があるかもしれません。AMは材料費も通常の樹脂ペレットよりも高いし、採算が取れる形で製造するには多くの要素を変更する必要があります。そこには多くの調整事項があります。担当者が一人で変えられる範囲を大きく超える場合が多いのです。JINSさんでも山本光学さんでもそうでしたが、意思決定者が現場推進者を支援し、取り組んでいくことが必要になると思います。
―確かに今やっている仕事に加えて、他の部門を動かすのはとても大きな壁ですね。
逆に経営層のコミットがあれば、社内に3Dプリンターに詳しい設計者や造形者がいなくても、サブスクリプションの中で、データも用意できますし、造形支援も受けられるので、実現できます。そういう取り組みを行っている人たちはとても高い熱量を持っています。そういった熱量があれば、3Dプリンターでいままでできなかったことができるかもしれません。
―では逆にCarbonを活用できない企業に関して教えてください。
設計変更ができず、材料がはまらず、意思決定者の協力が得られない場合です。例えば、単純に「設計変更できないが、金型レスでモノづくりしたい」といった場合、3Dプリンターの導入全般に対して言える事ですが、費用対効果を上げにくいと思います。またCarbonのサブスクリプション契約の中には、設計データの共有など、製品開発の重要な機密を共有しないと実現できないサービスもあります。例えばアプリケーションエンジニアによる設計に対する3Dプリンターならではの設計アドバイスや、既存の設計データをラティス構造化するサービスなどです。大手企業ほど、設計データの取り扱いは重要な機密として取り扱っている事は理解できます。Carbonが提供しているからといって、設計支援を活用する必要はもちろんありません。ですが、一緒にやろうと言っていただければ活用できるリソースを私たちはご用意しています。意思決定者の支援があれば、社外リソースを活用する座組を作りやすいでしょうし、関係部署との調整も担当者個人だけの責任で実施しなくて済むようになりますから、開発に専念できるのではないでしょうか。
AM推進は新規事業と似ている
CarbonというAMの前工程、造形工程を広範に支援してくれるパートナーと協業し、新しいモノづくりに取り組むことは新規事業に似ているかもしれない。工法を変える事は製造現場からするとリスク以外の何物でもないが、リスクを取るからこそ、結果を変えることができる。
現状の強みを活かした新しい価値の創造を言葉だけではなく実際のモノづくりに落とし込む一つのアプローチがAMへの取り組みだ。そしてリスクを最小化するための選択肢の一つが、機材だけではなく運用面の不安を一緒に解決しようとしてくれるチームを持つことだとおもわれる。Carbonのサブスクリプション契約はまさにそうした姿を実現しようとしている。そして実際に活用した企業の事例が続々生まれていることから、挑戦する価値があると言えるだろう。
ShareLab NEWS掲載ページはこちら