すべての消費者向け製品の真のテストは、実際の顧客がそれを購入するかどうかです。フォーカステスト、調査、直感ができることは限られています。消費者は、製品の機能を直接体験するまで、何をしたいのか分からないことがよくあります。優れた製品を創造するには、創造性、顧客からのフィードバック、およびデザインを繰り返す柔軟性が必要です。
プラスチック部品の設計を見直す場合、射出成形を変更する相当多くの資本とリードタイムが必要であるため、革新を妨げ、プロセスを遅らせかねません。NXT Outdoors™は、DrawLite™製品(引っ張って起動するサイトライト)にCarbonのSpeedCell™システムを活用し、この課題を克服しました。このケーススタディを読んで、製品の設計と生産サイクルをどのように加速させ、コストや品質を犠牲にすることなく顧客のフィードバックを迅速に統合する方法を学びましょう。
設計改良のコスト
屋外用品の革新者として、NXT Outdoors™のデザイナーとエンジニアは、自身の趣味に目を向け、インスピレーションと問題解決に役立てます。彼らは、アーチェリーの顧客と頻繁に問題を共有しました。例えば、暗い場所で照準を合わせるための照明付きボウ(弓)用照準器のバッテリー切れ(図1)。照準器を照らすにはトグルスイッチが必要でしたが、ついトグルをオフし忘れるのが常でした。射手は、トグルを切り替えなかった自分自身を責めていましたが、なぜ照準器がオフにならないのでしょうか?
「顧客からのフィードバックは製品改善には不可欠であり、Carbonの3D製造システムは、自由に設計改良できるこれまでにない柔軟性を提供してくれました。」
Bryan Rogers
NXT Outdoors メカニカルエンジニア
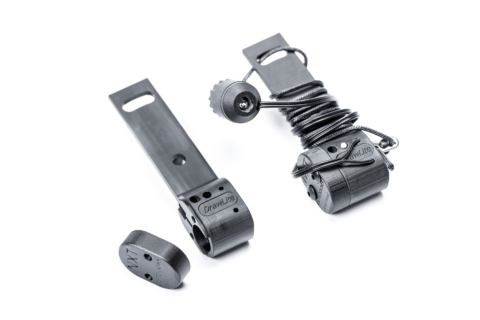
図1:Carbon SpeedCell™システムで造形したスイッチ本体とキャップ。右:NXT Outdoors™が販売するDrawLite™照明照準キット(スイッチハウジング、弓が引かれたときにスイッチを作動させるケーブル、アーチェリー場に取り付けられるライト)。
デザイナーは有望な解決策を試しました。ボウ(弓)を引いて制御するライトを照準器に取り付けました。彼らはそれを自分たちでテストし、金型に7万9000ドルを費やしました。製品に関する顧客からのフィードバックは好評でしたが、設置時間は約15分で、すべてのボウ(弓)の種類に対応できませんでした。取り付けが容易になり取り付け時間を短縮でき、製品がより多くの弓に対応できれば、デザイナーはユーザー体験を大幅に向上させられます。金型の再設計は5,000ドルから始まり、この見直しが最後とは思われませんでした。多くの消費者向け製造業者同様に、NXT Outdoors™は製品設計をより迅速に見直す必要がありました。
概念実証(Proof Of Concept)を通して探求
新しいソリューションを迅速に試作することは、業界での慣例です。従来NXT Outdoors™は、改善版ソリューションを設計し、生産用金型を修正していましたが、その代わりに、Carbonのソリューションを使用できました。
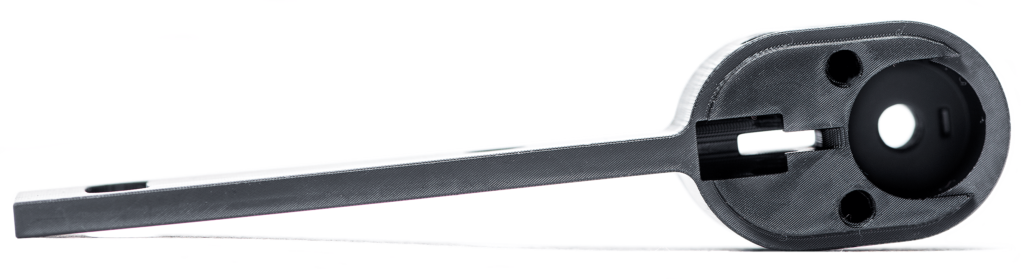
図2:ハウジング本体・キャップ無し。右側の大きな空洞でバッテリーと電子機器を保持。右隣接する2つの小さな穴はキャップをハウジングに対して保持するねじ止め。左側の大きな穴は回路を閉じアーチェリー場を照らす、引いて作動するスイッチを収納。
NXT Outdoors™のリードデザイナーTony SchwartzとメカニカルエンジニアBryan Rogersは、等方性、金型レスでの見直し、材質の品質面でSpeedCell™システムを有望な技術と見ていました。Carbonのプロセスは等方性パーツを実現するため、同じSpeedCell™システムを製品開発と量産の両方に使用しました。これにより、各々の機器での試作製品開発(例 SLA、FDMプリンタ)、量産オペレーション(例 射出成形、切削加工、真空注型)で発生する、一般的なプロセス上の課題を取り除きます。NXT Outdoors™は新しい顧客セグメントから多くの学びを期待していたので、金型を変えずに製品を変更できるのは魅力的でした。最後に、Bryanは、Carbonの硬質ポリウレタン(RPU)素材が、機械的、外観的、コスト的な特性を持っていると特定しました。
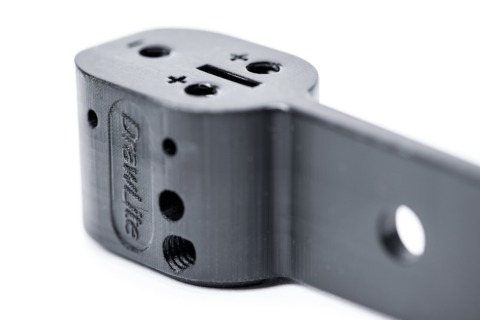
図3:造形した本体の底。造形したねじ山はDrawLite™ロゴの上。上向きの面に2つの対称の穴。
NXT Outdoors™の次の目標は概念実証(Proof Of Concept)を確立することでした。ハウジングのキャップと本体は、本体に取り付けられるすべての部品として、再加工する必要のある主要なプラスチック部品でした。射出成形用に最適化された元のデータをCarbonプリンタで造形し、最適な条件下での機械的性能を確認することから始まりました。最初の造形後、RPU部品が機械的品質と表面仕上げの点で有効な代替品になることは明らかでした。見直しプロセスを通じて、NXT Outdoors™は、より多くの設置仕様に対応するなど、より迅速かつ簡単に設置できるように、DrawLite™を再設計しました。さらには、内部のねじ山も造形できました。従来の射出成形では造形不可能であり、手作業でのねじ切りを要しました。
高品質部品の造形は始まりに過ぎませんでした。Carbonを使った新しいアプローチは、同社がどのように製品を市場に投入できるかという根本的な転換をもたらしました。試作品が量産品であったため、部品が認定されれば、より多くの部品を製造するためのリードタイムは必要ありませんでした。NXT Outdoors™は、リアルタイムで部品を製造し、販売することで、製品を即時に提供し、顧客のフィードバックを製品の設計に反映させられます。(従来の射出成形製造プロセスに関するコストをよりよく理解するためには、「射出成形の製造コスト」をご参照ください。)
コスト、スピード、または品質?3つすべてを同時に
NXT Outdoors™は、初期部品設計後に6回の設計改良を行いました(図2)。設計改良のたびごとに、機械的な改善、顧客のフィードバックによる新しい洞察、ボウ(弓)の幅広いモデルへの対応、Carbon造形プロセスに合わせた最適化を実施しました。新しいデザインにより、顧客の取り付け時間が20分以上から5分以下に短縮されました。その後の見直しでは、単一のキットを使用して、効率的に対応可能な、販売されているボウ(弓)モデルの対象を拡大しました。このキットは、右利き、左利きのボウ(弓)モデルと4種類の弦サイズに対応しました。この最適化により、1部品あたり約56分から38分まで造形時間が25%以上短縮されました。CarbonのSmart Part Washer™を使用した場合、洗浄時間はバッチあたり35分から6分に短縮され、80%以上削減されました。
NXT Outdoors™は、ユーザーに愛用されている特許出願中の革新的な照明付き照準器を開発しました。迅速な試作、迅速な生産、顧客へのフィードバックの収集と統合といった同社の理念をCarbon SpeedCell™システムと組み合わせてできたものです。また、ユーザー体験の大幅な向上、即生産できるパーツ、射出成形に匹敵するコストを実現しました。