世界中で毎年1,000万人が結核に罹患しています。内41%は、診断も報告もされておらず、治療もされていない可能性があり、その多くは新興国に住んでいます。 結核の診断と報告を改善する必要があるのは明らかです。最近では、世界保健機関が2016年のグローバル結核レポートで重大なギャップがあると強調しています。
「テクノロジーは現実の世界で私たちが持っているもののうち魔法に最も近いものであり、Global Goodはそれを最も必要とする人々、つまり経済的に最下層におり苦しんでいる10億人以上の人々の生活を変えるために、その独創的な魔法を使います。私たちは常に、アイデアをより迅速かつ低コストで市場にて実現する方法を模索しています。Carbonはその手助けとなっています。」
Nathan Myhrvold
Intellectual Ventures 創設者兼CEO
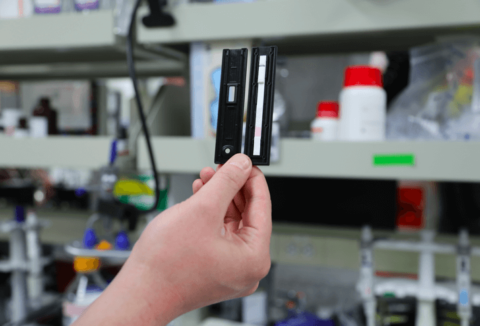
図 1:Carbon 技術で 3D プリントした結核診断カセット
Intellectual Ventures(IV)とBill Gatesが人道的に効果のあるテクノロジーを開発するために提携したGlobal Good Fundは、医療インフラが限られている国向けに使いやすく手頃な価格の早期結核診断デバイスを開発することにより、このギャップに対処しようとしています。 技術を生むためにCarbonと提携して、フィールドトライアルで使用できるデバイスをデザイン、設計、製造しました(図1)。 このケーススタディでは、Carbon技術が診断カセット製品の開発サイクルと製品化に要する時間を短縮し、世界中で命を救うためにどのように貢献したかを説明します。
課題
Global Goodは、IVラボの科学者たちと共に、発明のごく初期段階に焦点を当て、コンセプトを検証し、テクノロジーを改良して世界中に影響を与える可能性を示すなど、複数の研究分野で仕事をしています。このミッションに基づきGlobal Goodは、迅速で使いやすく、低コストの新しい正確な結核診断方法を開発したいと考えていました。
従来の診断方法は高価で時間がかかるため、新しい結核症例の大部分が発生する一方でリソースが不足している環境にはふさわしくありません。もう1つの課題は、結核診断プロセスに不可欠な痰の採取が高齢者、子供、HIV患者にとって難しいことと、その過程で病原体を運ぶエアロゾルを生成する可能性があるため、医療従事者にリスクを及ぼすということです。
製品開発—新しい設計アプローチ
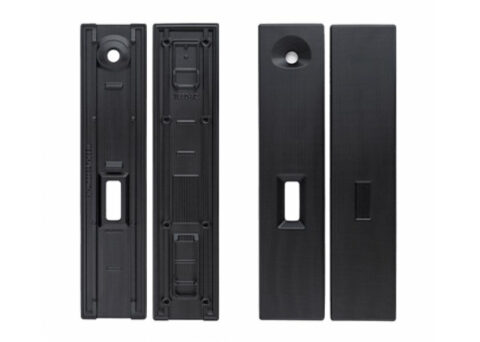
図2:側方流動ストリップは3Dプリントした診断カセットハウジング部品2つの間に位置する
チームは、マラリア診断、家庭内妊娠検査用に開発された使いやすい側方流動分析(LFA)テストにヒントを得、新製品のデザインを用いて、3つの課題の内迅速さと使い勝手という2つを解決する製品の開発に着手しました。痰のサンプルを必要とする代わりに、このデバイスは尿を使用し、結核のバイオマーカーを検出します。この新たな結核テスト案には、検出試薬がプラスチックカセット内に封入された側方流動ストリップも含まれます(図1、図2)。迅速な検出と痰を不要にという課題に対処する初回の設計案にとって、次の課題は、フィールド評価用にプラスチックカセットをコスト効率よくデザイン、設計、製造することでした。
製品開発—短期間で低コストを実現
新製品の開発では、初期段階での設計と試作の成功が課題です。IVラボの製品開発チームは、新しい設計方法を採用しただけでなく、イノベーションのスピードを上げることによって製品開発コストを大幅に削減しました。以前のIVラボ製品開発サイクルには(1)設計と試作、(2)金型開発、(3)射出成形品の製造、(4)フィールドテスト (図3)という4つの異なるフェーズがありました。IVラボチームは、熱溶解積層法(FDM)などの積層3Dプリント技術により試作品を製作後、射出成型の短時間運転によって最終部品の製作を行っていました。
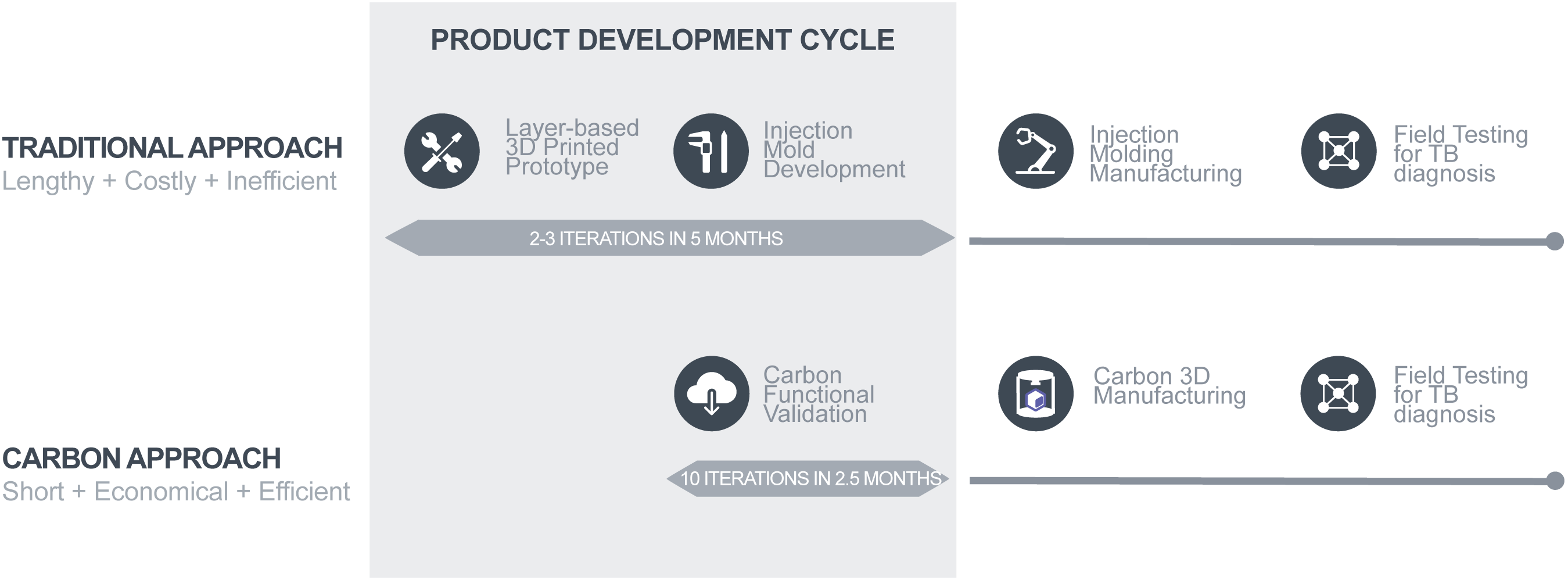
図3:カセット製品開発アプローチの比較:従来方式とCarbon
但し従来の技術では、既存の積層技術でのカセット試作はスピードが遅く、射出成形の金型改良には時間を要するうえそのコストは金型あたり通常25,000ドルと高価なため、チームは即座に問題にぶつかりました。その結果、IVラボチームは試作品の改良を2〜3回しか実行できず、その後2〜3回の射出成形の金型改良を経て、製品開発サイクルは全体で約5か月となりました(図3)。チームは、金型の不具合や金型修正に伴う遅延を数多く経験しました。これらの金型コストは、製品開発の固定費に大幅に上乗せされ、製品の改良を実行するうえでの経済的障壁となりました。リソースが不足する国向けに費用対効果の高い新製品を再設計するというミッションを勘案すると、これは望ましいことではありません。コストと時間のかかる製品開発プロセスに不満を抱いたIVラボチームは、より効率的な方法を検討することにしたのです。
IVラボは、製品開発チームがDigital Light Synthesis™技術を搭載したCarbonのMシリーズプリンタを紹介されたことによって、より良い製造方法を発見することとなりました。IVラボは、Carbonのエンジニアと緊密に連携して、Carbon材料の硬質ポリウレタン樹脂(RPU 70)により、最初のカセットデザインを1週間足らずで3Dプリントしました。Carbonの使いやすいソフトウエアと産業用プリンタ設計により、IVラボのエンジニアは迅速に作業を進め、製品設計の改良をすぐに開始できるようになりました。Carbonのエンド・ツー・エンドのデジタルマニュファクチュアリングプロセスにより、IVラボのエンジニアは、従来のやり方と比較して半分の時間で製品設計改良を10回実施しました(図3)。更には、3D製造はオンデマンドのため、材料の無駄が最小限に抑えられ、部品の最小発注数量の制約がなく、部品在庫を維持する必要もありません。
IVラボが、製品開発サイクル全体を通して同じ装置と同じ材料で、製品の改良、機能検証、実際の製造を行えることは、Carbon製造技術の重要な利点の一つです。従来の製造では、各段階で異なる材料、異なる技術が必要となるため、フレキシビリティが低下し、大幅な遅延が発生し、運用効率が低下してしまいます。Carbon<技術を活用して、IVラボは製品設計の改良回数を2〜3倍に増やしつつ、最終製品のコストを大幅に削減することができました。コスト削減は、新興国向けの低コストソリューションを実現するという使命を持つIVラボにとって驚異的な成果となります。
まとめ
3D製造は変革の道のりであり、IVラボの製品開発チームは、時間のかかる試作と非効率な従来の製造方法から、Carbonによる迅速で効率的な3D製造方法へと見事に躍進しました。IVラボチームは3D製造による結核診断テストのフィールドテストを1,000回以上行い、成功を収めました。人道的に最も困難な問題を解決するテクノロジーを発明するという使命の下、Global GoodとIVラボチームは、Carbon技術を活用して使いやすい低コスト製品を提供することによって、結核の迅速な診断への貢献と、致命的な病気を撲滅する道を開くことへの支援を実現します。